آهن زنگ نزن | انواع فولاد ضد زنگ
دسترسی سریع به محتوای مقاله
آهن زنگ نزن یا همان فولادهای ضد زنگ به دسته ای از خانواده فولادها گفته می شود که مقاومت در برابر خوردگی، مهم ترین مشخصه آنها است. انواع آهن زنگ نزن با مقادیر متفاوتی از کروم و سایر عناصر آلیاژی، از یکدیگر متمایز می شوند.
اما به طور کلی، فولادهای ضد زنگ یا استنلس استیل، فولادهایی هستند که حداقل 10.5 درصد کروم دارند. انواع استیل ضد زنگ بر اساس نوع ریزساختار آنها در دمای اتاق، شامل استیل آستنیتی، فریتی، مارتنزیتی، دو فازی و رسوب سخت می شوند. در ادامه، به بررسی هر یک از این انواع استنلس استیل خواهیم پرداخت.
انواع آهن زنگ نزن
فولادهای زنگ نزن بر اساس نوع ریزساختار در دمای اتاق، به گروههای 5 گانه تقسیم میشوند. این ریزساختارها شامل فازهای پایدار آستنیت، فریت، مخلوط فریت- آستنیت (دو فازی) ، مارتنزیت و یا یک ساختار سخت شده حاوی ذرات ریز رسوبی است.
آهن زنگ نزن فریتی
استنلس استیل فریتی فقط حاوی کروم به عنوان عنصر اصلی آلیاژی است. مقدار کروم موجود بین 10.5 تا 30 درصد است. آنها به دلیل مقاومت متوسط در برابر خوردگی و خواص ساخت ضعیف شناخته شدهاند. خواص ساخت را میتوان با تغییرات آلیاژی بهبود بخشید و در گریدهایی مانند 434 و 444 این پارامتر رضایت بخش است.
انواع آهن زنگ نزن فریتی مطابق با استاندارد AISI، شامل سری 400 می شوند. به منظور آشنایی با گریدهای فولاد ضد زنگ به این لینک مراجعه نمایید.
فولادهای ضد زنگ فریتی نمیتوانند با عملیات حرارتی سخت شوند و همیشه در شرایط آنیل استفاده میشوند. آنها مغناطیسی هستند و در بازار به استیل بگیر یا فولاد بگیر معروف اند و همچنین مستعد ترکخوردگی تنشی نیز نیستند. ضمن اینکه مقاطع نازک از استیل فریتی قابلیت جوشپذیری قابل قبولی دارند اما با افزایش ضخامت مقطع، این ویژگی در آنها کاهش مییابد.
به نظر شما تفاوت استیل بگیر و نگیر چیست؟ در ادامه به معرفی استیل نگیر نیز خواهیم پرداخت.
یکی از مشکلات رایج در استفاده از آهن های زنگ نزن فریتی، تردی دمای 475 درجه سانتیگراد است. این پدیده متناسب با محتوای کروم است و در محدوده دمایی 425 - 550 درجه سانتیگراد رخ میدهد.
این امر نتیجه تجزیه فریت به دو فاز شامل فاز غنی از کروم و فاز غنی از آهن است. هرچه آلیاژ غنی از کروم باشد، واکنش سریعتر خواهد بود.
پیامدهای این واکنش اساساً در خوردگی انتخابی فاز غنی از آهن است. برای جلوگیری از این نوع شکنندگی، دمای سرویس قطعه باید همیشه حداکثر تا 400 درجه سانتیگراد محدود شود.
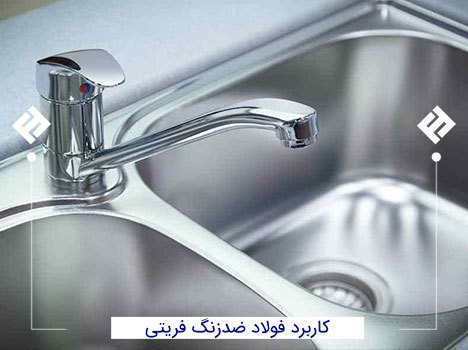
آهن زنگ نزن آستنیتی
استیل های آستنیتی حدود 16 تا 25 درصد کروم و 8 تا 26 درصد نیکل دارند. فولادهای آستنیتی متداول ترین فولادهای ضد زنگ هستند که براساس استاندارد AISI، به زیر مجموعه های سری 300 و سری 200 تقسیم می شوند.
تفاوت سری 200 و 300 در این مورد است که سری 300 حاوی نیکل بالا است اما در برخی از سری های 200، منگنز جایگزین نیکل شده است. استیل های آستنیتی بهترین نوع فولادهای ضد زنگ به منظور مقاومت در برابر خوردگی هستند چون که حضور نیکل در آنها باعث پایداری آستنیت میشود. تاثیر عناصر آلیاژی بر فولاد ها را در این لینک مطالعه نمایید.
با افزودن عناصری مانند مولیبدن، تیتانیوم یا مس میتوان خواص فولاد را تغییر داد. این تغییرات میتواند فولاد را برای کاربردهای دمای بالا مناسب کرده یا مقاومت در برابر خوردگی را افزایش دهد. اکثر فولادها نیز در دماهای پایین شکننده میشوند اما نیکل موجود در انواع فولاد ضد زنگ آستنیتی، با کاهش دمای DBTT یا همان دمای انتقال نرمی به تردی، آن را برای کاربردهای دما پایین مناسب میکند.
در واقع باید گفت که استنلس استیل آستنیتی، DBTT ندارد. استیل آستنیتی به طور کلی غیر مغناطیسی است و در بازار به استیل نگیر یا فولاد نگیر معروف است. همچنین، آنها قابلیت سخت کاری با عملیات حرارتی را ندارند و برای این منظور باید از فرآیندهای کارسرد استفاده کرد.
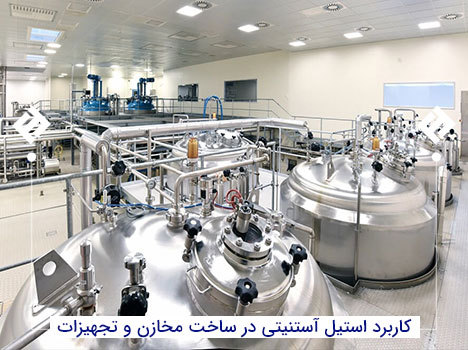
آهن زنگ نزن مارتنزیتی
مشابه با استیل فریتی، انواع فولاد ضد زنگ مارتنزیتی نیز بر اساس استاندارد AISI، شامل سری 400 هستند. آنها دارای کربن کم تا متوسط به میزان 1.2 درصد بوده و حاوی 10.5 تا 18 درصد کروم هستند. اگرچه که خواص مقاوم به خوردگی آنها مناسب است، اما هر زمان که استحکام مکانیکی مهمتر از مقاومت به خوردگی باشد، از این فولادها استفاده میشود.
خواص مقاوم به خوردگی استیل مارتنزیتی ضعیفتر از سایر انواع فولاد ضد زنگ است. فولادهای مارتنزیتی همچنین مغناطیسی هستند و از شکل پذیری و چقرمگی نسبتاً بالایی برخوردارند که شکلدهی آنها را آسان میکند.
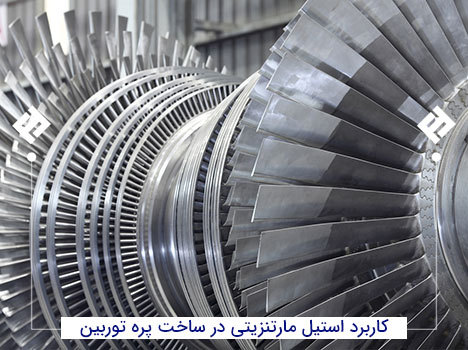
آهن زنگ نزن داپلکس (دو فازی)
آهن زنگ نزن داپلکس دارای محتوای کروم بالا و نیکل کمی هستند و ساختار آنها شامل مخلوطی از هر دو فاز آستنیت و فریت است. استیل های داپلکس در برابر ترکخوردگی ناشی از تنش مقاوم هستند، اما به اندازه فولادهای ضدزنگ فریتی نیستند.
همچنین، چقرمگی فولادهای داپلکس نسبت به گریدهای فریتی بالاتر بوده اما نسبت به گریدهای آستنیتی کمتر است. ضمن اینکه، فولاد ضد زنگ داپلکس به راحتی جوش داده میشود و دارای مقاومت کششی بالایی نیز هستند. جوشکاری فولاد ضد زنگ نیاز به دانش و مهارت بالایی دارد و باید توسط افراد ماهر انجام شود.
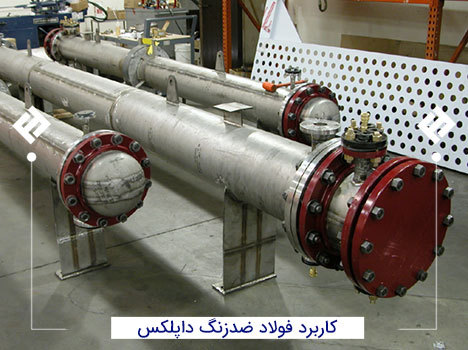
آهن زنگ نزن رسوب سخت شونده (PH)
استیل رسوب سخت (precipitation hardening) که به اختصار PH نامیده میشود، حاوی هر دو نوع عناصر کروم و نیکل است که با اعمال عملیات حرارتی، سختی آنها به مقدار چشمگیری افزایش مییابد.
با انجام عملیات محلولسازی، استیل های رسوب سخت قابلیت ماشینکاری پیدا کرده و سپس در دمای پایین میتوانند رسوبسخت شوند و هیچگونه اعوجاجی در ساختار آنها ایجاد نمیشود. این گرید ها دارای بیشترین استحکام کششی در بین تمام فولادهای ضد زنگ هستند. با انواع عملیات حرارتی فولاد ها در این لینک آشنا شوید.
کاربرد انواع فولاد ضد زنگ
با توجه به خواصی همچون مقاومت به خوردگی، مقاومت در برابر ضربه، مقاومت در برابر دمای بالا و پایین و نیز استحکام بسیارخوب، انواع آهن زنگ نزن در کاربردهای مختلف صنعتی مورد استفاده قرار میگیرند که شامل موارد زیر میشوند:
- خودرو و حمل و نقل
- فناوری پزشکی
- ساخت و ساز
- ساخت هواپیما
- صنایع غذایی و پذیرایی
- ساخت تانکرها و مخازن ذخیره
- ساخت کشتی
سوالات متداول
1- انواع فولاد ضد زنگ کدام اند؟
فولادهای ضد زنگ براساس نوع ریزساختار به انواع فریتی، آستنیتی، مارتنزیتی، داپلکس یا دو فازی و رسوب سخت تقسیم می شوند.
2- کدام نوع آهن زنگ نزن بهترین مقاومت خوردگی را دارد؟
استیل های آستنیتی بهترین نوع فولاد ضد زنگ جهت مقاومت به خوردگی هستند چون وجود نیکل باعث پایداری آستنیت می شود که عامل مقاومت به خوردگی است.
3- مقاوم ترین فولاد زنگ نزن کدام است؟
فولاد ضد زنگ رسوب سخت یا PH مستحکم ترین نوع استیل است و پس از آن نیز استیل مارتنزیتی مستحکم ترین است.