با صفر تا صد فرآیند آهنگری آشنا شوید
دسترسی سریع به محتوای مقاله
وقتی صحبت از آهنگری میشود، ناخودآگاه ذهن به سمت فردی میرود که با در دست داشتن یک چکش فولادی، به ضربه زدن به یک قطعه آهن برای شکلدهی به آن مشغول است. آهنگری یکی از قدیمیترین روشهای شکلدهی مواد است که امروزه کمتر بهصورت دستی و اغلب با استفاده از چکشهای مکانیکی بزرگ انجام میشود. این فرآیند در نگاه اول ساده به نظر میرسد اما حاوی تنوع بالایی ازنظر فرآیند تولید و دمای کاری است.
ازآنجاییکه یکی از فاکتورهای تاثیرگذار بر قیمت آهن آلات روش تولید آنهاست، بهینهسازی روش تولید، شناخت دقیق پارامترهای دخیل در آن و... امری ضروری است. در اینجا به اصول فرآیند آهنگری فلزات و آلیاژها، انواع روشهای موجود و محصولاتی که به روش آهنگری تولید میشوند اشاره خواهیم کرد.
آهنگری چیست؟
آهنگری یا فورج کردن (Forging) یک روش شکلدهی برای ساخت ابزار با آهن و دیگر فلزات و مبتنی بر اعمال نیروی فشاری موضعی با استفاده از چکشهای دستی یا مکانیکی و هیدرولیک است.
در مقایسه با سایر روشهای ساخت و تولید، آهنگری منجر به تولید قطعات فلزی مستحکمتری میشود. چراکه در طی این فرآیند، فلز گرم و فشرده شده و ترکها و فضاهای خالی در ساختار قطعه فشرده و بسته میشوند. ضمن اینکه، این فرآیند چندمنظوره است و میتوان آن را بر روی قطعات کوچک با اندازه چند اینچ تا اجزای بزرگ که بیش از 30 تن وزن دارند، استفاده کرد.
فرآیند آهنگری داغ همچنین ناخالصیهای موجود در فلز را تجزیه کرده و آنها را در سراسر قطعه توزیع میکند. این امر در جلوگیری از انباشت و تمرکز آخالها در قسمت خاصی از قطعه مؤثر است. آخالها مواد مرکبی هستند که در طی فرآیند تولید در ساختار فولاد ایجاد میشوند و تمرکز تنش و افت خواص در قطعات آهنگری نهایی را به دنبال دارند.
فرآیند آهنگری منجر به تصفیه یا پالایش بهتر قطعات ازنظر ریزساختاری میشود. همچنین، آهنگری منجر به تغییر ساختار دانه در فلز میشود. از طریق این فرآیند، دانهبندی مواد فلزی در هنگام تغییر شکل تغییر کرده و ساختار دانهای مطلوبتری ایجاد میشود که درنتیجهی آن، استحکام فلز بیشتر افزایش مییابد.
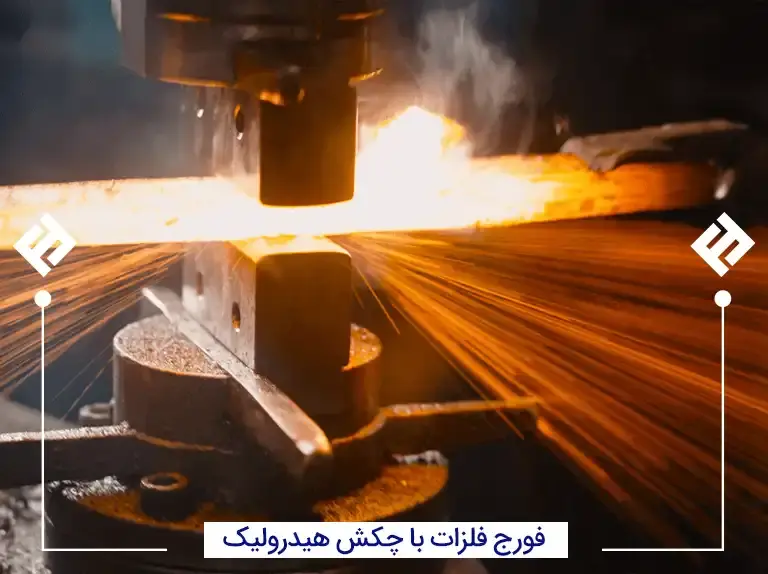
کدام فلزات را میتوان فورج کرد؟
ازآنجاییکه تمام فلزات میتوانند تحت تأثیر حرارت و فشردهسازی قرار گیرند، توسط فرآیند آهنگری میتوان تقریباً هر فلزی را شکل داد. بسیاری از تولیدکنندگان به دلیل توانایی این فرآیند در تولید قطعات با کیفیت مکانیکی بالا و حداقل ضایعات، آهنگری را انتخاب میکنند. هدف از این فرآیند تغییر شکل فلزات به یک هندسه مشخص است و به آنها مقاومت در برابر خستگی و استحکام میدهد. درحالیکه بیشتر فلزات را میتوان آهنگری کرد اما فولادهای کربنی، فولادهای آلیاژی و فولادهای ضد زنگ بیشترین استفاده را دارند.
کدام فلزات را نمیتوان فرج کرد؟
برخی از فلزات و آلیاژها مانند چدن و برخی از فولادهای پرکربن به دلیل شکلپذیری محدود، قابلیت آهنگری ندارند. علاوه بر این، برخی از فلزات مانند آلیاژهای با استحکام بالا ممکن است برای تحمل فرآیند آهنگری بیشازحد شکننده باشند.
مزایا و معایب فرآیند فورجینگ
آهنگری یک فرآیند تولیدی است که مزایای زیادی ازجمله افزایش استحکام کششی نسبت به قطعات ریختهگری، افزایش استحکام خستگی و مقاومت در برابر خزش را به دنبال دارد. همچنین، عملیات آهنگری کمهزینه است و نیازی به اپراتور ماهر ندارد. ضمن اینکه، با این روش میتوان قطعات را در ابعاد مختلف از کوچک تا بزرگ تولید کرد.
از معایب این روش میتوان به قیمت بالای محصولات تولیدی نسبت به سایر روشها اشاره کرد. همچنین، برای دستیابی به سطح مناسب، عملیات پرداخت ثانویه موردنیاز است. فرمهای پیچیده را نمیتوان با آهنگری تولید کرد و اندازه قسمت آهنگری محدود به ظرفیت پرس است. در نهایت، باید اشاره کرد که فلزات شکننده را نمیتوان آهنگری کرد و استفاده از آنها را به تعداد معدودی از کاربردها محدود میکند.
انواع فرآیند آهنگری یا Forging
آهنگری بر اساس دمای کاری فرآیند به دو دسته آهنگری داغ و آهنگری سرد تقسیم میشود. این دو روش ازنظر خواص محصول، کیفیت و هزینه تمامشده متفاوت از یکدیگرند. آهنگری سرد نیازمند الزامات پیچیدهتری بوده و معمولاً روش آهنگری داغ به دلیل سادگی و ارزانتر بودن ترجیح داده میشود.
آهنگری داغ Hot Forging
آهنگری داغ نیازمند حرارت دادن فلز بالاتر از دمای تبلور مجدد آن است که برای فولادها حدود 1260 درجه سانتیگراد است. مزیت اصلی فورج گرم، کاهش انرژی موردنیاز برای شکلدهی بهتر فلز است. به این دلیل که گرمای زیاد، استحکام تسلیم را کاهش میدهد و شکلپذیری فلز را بهبود میبخشد. همچنین، به دلیل انجام فرآیند پالایش دانهها در فورج گرم، ناهماهنگیهای ریزساختاری در محصولات حاصل از آن حذف شده یا کاهش مییابند.
آهنگری سرد Cold Forging
آهنگری سرد معمولاً به فورج کردن فلز در دمای اتاق اشاره دارد. اگرچه در هر دمایی کمتر از دمای تبلور مجدد فلز نیز امکانپذیر است. بسیاری از فلزات، مانند فولاد پرکربن برای آهنگری سرد بسیار قوی هستند. به عبارتی، استحکام بالای آنها فرآیند شکلدهی این فلزات را در دماهای پایین دشوار میکند. از طرفی، آهنگری سرد کنترل ابعادی دقیقتر، یکنواختی بیشتر محصول و پرداخت سطح بهتری را ارائه میدهد. بااینحال، این افزایش تطبیقپذیری هزینه دارد، زیرا آهنگری سرد به تجهیزات قدرتمندتری نیاز دارد و ممکن است نیاز به استفاده از آنیلهای میانی نیز باشد.
انواع روش های آهنگری فلزات
با اینکه آهنگری ازنظر دمای فرآیند شامل دو نوع گرم و سرد میشود اما این فرآیند ازنظر روش انجام کار نیز به انواع مختلفی تقسیم میشود. رایجترین انواع روشهای آهنگری فلزات عبارتاند از:
- آهنگری قالب باز (Open Die Forging Process)
- آهنگری قالب بسته (Closed Die Forging Process)
- آهنگری پرسی (Press Forging Process)
- آهنگری غلتکی (Roll Forging Process)
- آهنگری کله زنی (Upset Forging Process)
- آهنگری ایزوترمال (Isothermal Forging Process)
آهنگری قالب باز
زمانی فرآیند فورج بهوسیله قالبهای مسطحی که پروفیلهای از پیش برش خوردهای ندارند انجام شود، به آن آهنگری قالب باز میگویند. طراحی قالب باز به فلز اجازه میدهد تا در همهجا جریان یابد، بهجز جایی که قالب را لمس میکند. برای دستیابی به بهترین خواص و نتایج، طول این قالب باید حدود 30 سانت باشد. فورج قالب باز قطعاتی با مقاومت و استحکام بیشتر در برابر خستگی ایجاد میکند و احتمال بروز خطا یا ایجاد سوراخ در قطعه را کاهش میدهد. همچنین میتوان از آن برای رسیدن بهاندازه دانه ریزتر نسبت به سایر فرآیندها استفاده کرد.
آهنگری قالب بسته
در این روش، قالبها را به سندان متصل میکنند و با استفاده از ضربات چکش، فلز درون قالب جریان مییابد. هزینههای بالای ابزارآلات اولیه منجر به هزینهبر بودن این فرآیند برای تولید در مقیاس پایین میشود، اما با افزایش قطعات تولیدی، فرآیند آهنگری قالب بسته مقرونبهصرفه میشود. فورج قالب بسته استحکام فوقالعادهای نسبت به روشهای دیگر ارائه میدهد. از کاربردهای رایج فورج قالب بس ته میتوان به تولید قطعات خودرو و ابزارآلات اشاره کرد.
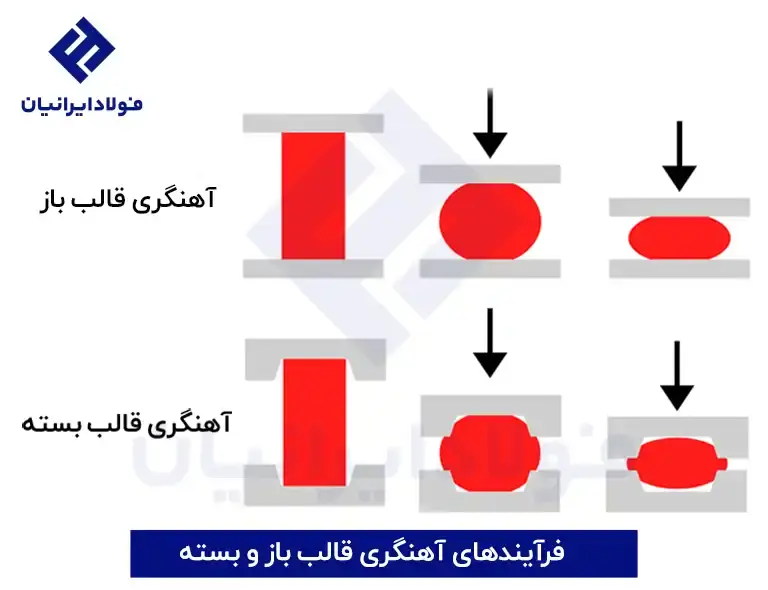
آهنگری پرسی
آهنگری معمولی شامل ضربات چکش بهصورت دستی یا اتوماتیک است اما در آهنگری پرسی عامل اصلی شکلدهی، فشردهسازی با استفاده از فشار مداوم و ممتد است. در این روش، فلز روی یک قالب ثابت قرار میگیرد و بازوی فشاری، فشار مداوم را اعمال میکند تا قطعه به شکل دلخواه برسد. در فورج پرسی، زمان تماس فلز با قالبها به طور قابلتوجهی طولانیتر از سایر انواع آهنگری است، اما فرآیند آهنگری پرسی از اینکه میتواند به طور همزمان کل محصول را تغییر شکل دهد، برخلاف یک بخش موضعی، سود میبرد.
یکی دیگر از مزایای فورج پرسی، توانایی کنترل نرخ تراکم است. کاربردهای فورج پرسی بسیار زیاد است، زیرا هیچ محدودیتی برای اندازه محصولی که میتوان ایجاد کرد وجود ندارد. فورج پرسی میتواند بهصورت گرم یا سرد انجام شود.
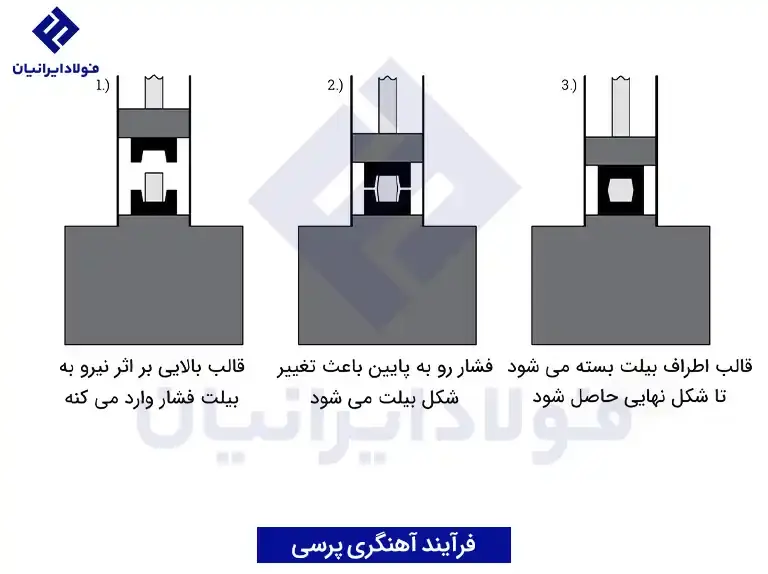
آهنگری غلتکی
روش آهنگری غلتکی حاوی استفاده از یک سری غلتکهای شکلدهنده فشاری است که بهوسیله آنها میلههای طویل تولید میکنند. در این فرآیند، میلههای فلزی گرم شده بین دو رول استوانهای با شیارهای مشخص قرار داده میشوند و با چرخش و اعمال فشار پیشرونده، بر طول میله افزوده شده و از قطر آن کاسته میشود. از مزایای این روش آهنگری میتوان به دستیابی به ساختار دانهای مطلوب اشاره کرد.
لازم به ذکر است با اینکه این فرآیند از غلتکها برای فرم دهی به مواد استفاده میکند، اما یک فرآیند آهنگری محسوب میشود و در دسته فرآیندهای نوردی جای نمیگیرد. فورج رول اغلب برای ساخت قطعات خودرو استفاده میشود.
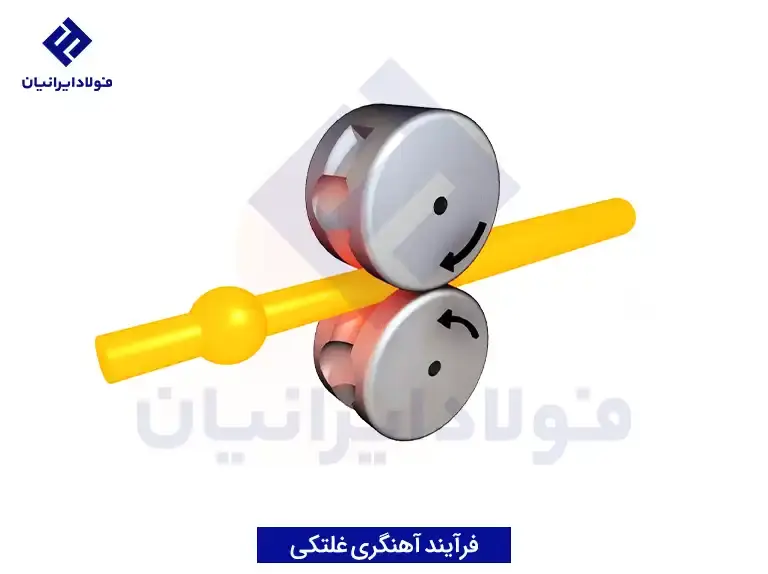
آهنگری کله زنی
این نوع فرآیند آهنگری معمولاً برای تولید پیچها استفاده میشود. ابتدا یک میله از یک سمت حرارت دهی شده و سپس در قالب قرار میگیرد تا با اعمال فشار اولیه، شکل لبه آن عوض شده و بهصورت کلاهک شود. سپس مجدداً وارد قالب شده و با اعمال فشار، شکل ششضلعی در قسمت سر میله ایجاد میشود. آهنگری Upset سرعت تولید بالایی داشته و میزان هدر رفت مواد و تولید ضایعات آن بسیار کم است.
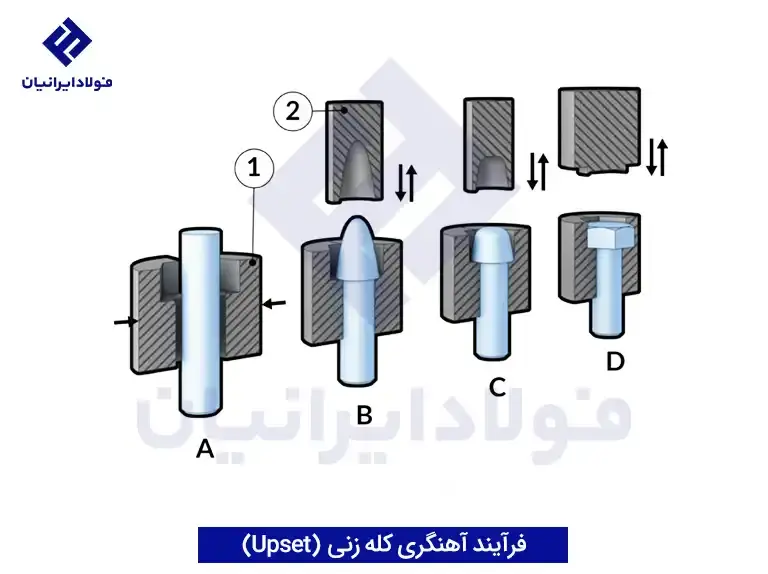
آهنگری ایزوترمال
آهنگری ایزوترمال فرآیند آهنگری است که در آن مواد و قالب تا یک دمای یکسان گرم میشوند. این نام از واژه "iso" به معنای "برابر" گرفته شده است. این روش معمولاً برای آهنگری آلومینیوم استفاده میشود و دمای کاری آن نسبت به سایر فلزات مانند فولاد کمتر است. دمای آهنگری برای آلومینیوم حدود 430 درجه سانتیگراد است، درحالیکه فولادها دمای حدود 930 تا 1260 درجه سانتیگراد را تجربه میکنند.
از مزایای این روش میتوان به کاهش نیاز به ماشینکاری و درنتیجه نرخ ضایعات پایینتر اشاره کرد. همچنین، به دلیل تلفات حرارتی کمتر، میتوان از ماشینهای کوچکتر برای آهنگری استفاده کرد. از معایب آهنگری ایزوترمال میتوان به هزینههای مواد قالب برای کنترل دما و فشار، نیاز به سیستمهای گرمایشی یکنواخت و نرخ پایین تولید اشاره کرد.
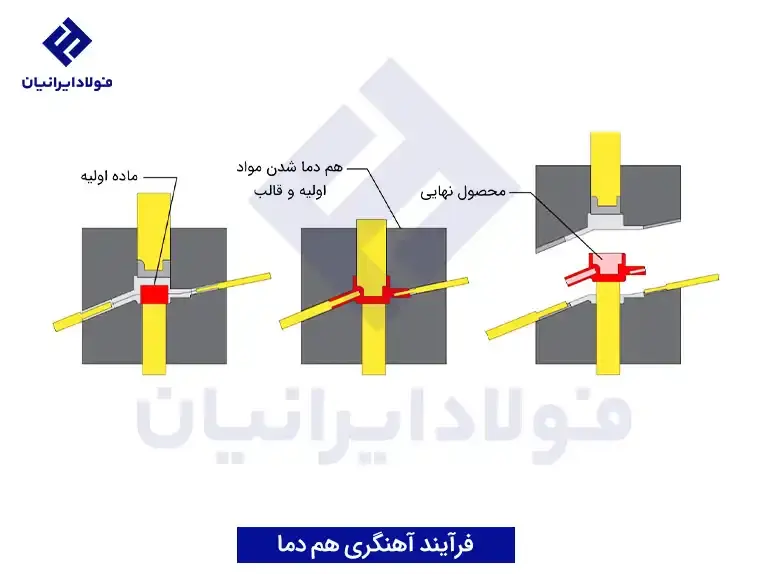
کاربردهای آهنگری یا فورجینگ
در برخی موارد، شکلپذیری و استحکام مواد را میتوان با فرآیند آهنگری کنترل کرد. همچنین، قطعات کوچک تا بزرگ را میتوان با این روش تولید کرد. حتی در مواردی که تولید قطعات به روش اکستروژن نیز امکانپذیر است، با استفاده از آهنگری می توات قطعات ضخیمتر با ضایعات کمتر تولید کرد. از مهمترین کاربردهای آهنگری میتوان به موارد زیر اشاره کرد:
- قطعات هواپیما
- قطعات اتومبیل
- ریل راهآهن
- میللنگ
- اهرمها
- چرخدندهها
- میلههای اتصال
- ساخت ابزار مانند پرچ، میخ، پیچ و مهره
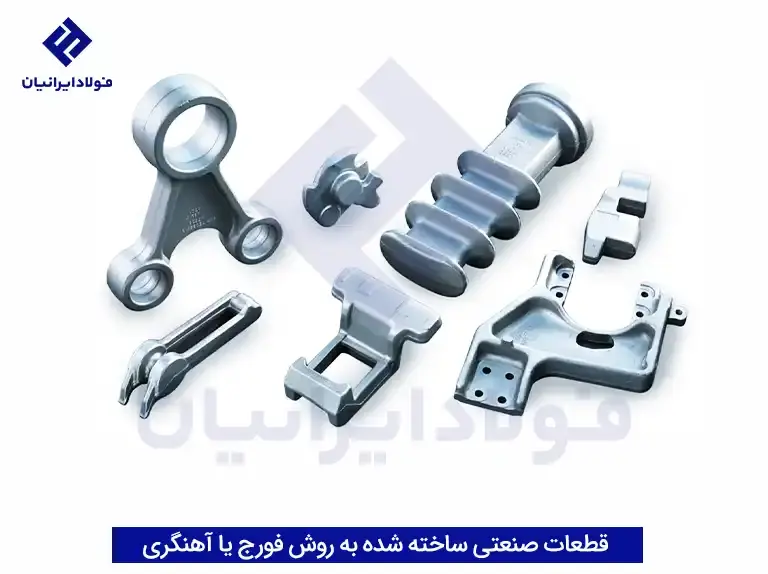
سؤالات متداول
1- فورجینگ چیست؟
آهنگری یا فورجینگ به فرآیند شکلدهی فلزات بهوسیله اعمال فشار موضعی با ضربه زدن به فلز توسط چکشهای دستی، هیدرولیک یا توسط غلتکهای شکلدهی گفته میشود.
2- انواع روشهای آهنگری فلزات کداماند؟
فورج قالب باز، فورج قالب بسته، فورج فشاری، فورج غلتکی، فورج کله زنی و فورج ایزوترمال از رایجترین فرآیندهای آهنگری هستند.
3- کدام فلزات را میتوان فورج کرد؟
فلزاتی مانند فولادهای کربنی، فولادهای آلیاژی و فولادهای ضد زنگ بهترین مواد برای شکلدهی به روش فورجینگ هستند. فلزاتی مانند چدن و برخی از فولادهای پرکربن به دلیل تردی بیشازحد قابلیت فورج کردن ندارند.