مهم ترین و کاربردی ترین روش های تقویت میلگرد
دسترسی سریع به محتوای مقاله
خوردگی میلگرد در بتن یک مشکل جهانی است که باعث ایجاد طیفی از مسائل اقتصادی، زیباییشناختی و کاربری میشود. بااینحال، اگر اثرات خوردگی در مرحله طراحی در نظر گرفته شود و تصمیمات، درست قبل از ساختوساز گرفته شوند، میتوان ساختمانهایی را ساخت که مقاومت بیشتری را در برابر خوردگی ارائه کنند. در همین راستا، انواع روشهای تقویت میلگرد نیز گسترش داده شدند.
خوردگی میلگرد در بتن در محیطهای خشن، بهویژه در مناطق ساحلی، استوایی یا بیابانی که دارای سطوح بالای نمک بوده و یا دمای شدید را تجربه میکنند، میتواند سریعتر اتفاق افتد. معمولاً، بخشهایی که بیشتر در معرض دید قرار میگیرند، زودتر خورده میشوند. بااینحال، بیشتر آرماتورهای خورده شده قابلمشاهده نیستند و ممکن است خوردگی فعال در یک میلگرد، 5 تا 15 سال قبل از شروع ترک در بتن طول بکشد.
خوردگی تا حدودی بر تمام ساختمانها و سازههای بتنی در سراسر جهان تأثیر میگذارد و هزینه تخمینی سالانه آن میلیاردها دلار برای اقتصادهای ملی است. بنابراین، مهم است که صاحبان داراییهای با ارزش بالا پیامدهای پرهزینه ناشی از نادیده گرفتن اثرات خوردگی بر ساختمانها و سازههای بتنی را درک کنند. درنتیجه، انتخاب راههایی برای جلوگیری و یا به حداقل رساندن ضررهای ناشی از خوردگی میلگردها امری حیاتی تلقی میشود. بنابراین، نیاز است تا انواع روشهای تقویت میلگرد مورد ارزیابی و اجرا قرار گیرند.
خوردگی میلگرد تحت چه شرایطی اتفاق میافتد؟
برای وقوع انواع خوردگی، یک سری عناصر و شرایط محیطی باید بهطور همزمان در محل حضور داشته باشند. که این عوامل در زیر آمده است:
- وجود حداقل دو فلز (یا دو مکان روی یک فلز واحد) که در سطوح مختلفی از انرژی باشند.
- یک الکترولیت
- یک اتصال فلزی
میلگردها ممکن است در بتن مسلح، دارای مناطقی باشند که در سطوح مختلفی از انرژی قرار داشته باشند. در اینجا، بتن بهعنوان الکترولیت عمل میکند و اتصال فلزی توسط خود میلگرد ایجاد میشود. خوردگی یک فرآیند الکتروشیمیایی است که شامل جریان بارها (الکترونها و یونها) میشود.
در مکانهای فعال بر روی میلگرد که آند نامیده میشوند، اتمهای آهن الکترونهای خود را از دست میدهند و بهعنوان یونهای آهن وارد بتن اطراف میشوند. این فرآیند واکنش اکسیداسیون نیمه سلولی یا واکنش آندی نامیده میشود و بهصورت زیر نمایش داده میشود:
2Fe = 2Fe2+ + 4e-
الکترونها در میلگرد باقی میمانند و به سمت محلهایی به نام کاتد جریان مییابند که در آنجا با آب و اکسیژن موجود در بتن ترکیب میشوند. واکنشی که در کاتد انجام میشود را واکنش کاهشی مینامند. یک واکنش کاهش رایج در خوردگی میلگرد فولادی عبارت است از:
2H2O + O2 + 4e- = 4OH-
برای حفظ قانون خنثی بودن الکتریکی، یونهای آهن از طریق آب موجود در منافذ بتن، به این مکانهای کاتدی مهاجرت میکنند و در آنجا ترکیب میشوند و هیدروکسید آهن یا زنگ آهن را تشکیل میدهند:
2Fe2+ + 4OH- = 2Fe(OH)
این هیدروکسید رسوب شده اولیه تمایل دارد تا با اکسیژن واکنش بیشتری انجام دهد و اکسیدهای بالاتری را تشکیل دهد. افزایش حجم زنگ آهن با واکنش بیشتر محصولات واکنش با اکسیژن محلول، منجر به تنش داخلی در بتن میشود که ممکن است برای ایجاد ترک و پوستهشدن پوشش بتنی کافی باشد.
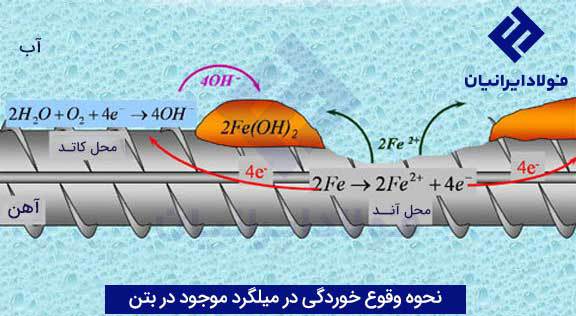
عوامل اصلی ایجاد خوردگی در میلگرد
pH بالا (قلیایی) بتن یک لایه غیرفعال بر روی سطح میلگردهای فولادی تقویتکننده ایجاد میکند که از خوردگی آنها جلوگیری کرده و یا آن را به حداقل میرساند. کاهش pH بتن توسط کربناته شدن یا ورود کلریدها (نمک)، دو عامل رایج خوردگی میلگردها در بتن، باعث تخریب لایه غیرفعال فولاد میشود.
کربناته شدن نتیجه حل شدن دیاکسید کربن (CO2) در منافذ بتن است که با کلسیم از هیدروکسید کلسیم [Ca(OH)2] و هیدرات سیلیکات کلسیم در سیمان واکنش داده و کلسیت (CaCO3) تشکیل میدهد. در مدتزمان نسبتاً کوتاهی، سطح بتن تازه با CO2 هوا واکنش نشان میدهد. بهتدریج، فرآیند به عمق بتن نفوذ میکند. پس از یک سال یا بیشتر، بسته به نسبت آب به سیمان، کربناته شدن معمولاً ممکن است به عمق 1 میلیمتر برای بتن متراکم با نفوذپذیری کم یا تا 5 میلیمتر برای بتن متخلخل و نفوذپذیرتر برسد.
کلریدها، معمولاً از محلهای در کنار دریا یا بهوسیله باد، بهمرورزمان به داخل بتن متخلخل مهاجرت میکنند. درنهایت، غلظت کلریدها درجایی که آرماتور فولادی قرار دارد به حد بحرانی میرسد. همچنین، در سازههای بتنی قدیمیتر، کلرید کلسیم (CaCl2) ممکن است در زمان ساخت بهعنوان تسریعکننده مجموعه بتن استفاده شده باشد.
هنگامیکه لایه غیرفعال تخریب میشود، میلگرد فولادی در حضور اکسیژن و رطوبت خورده میشود. با خوردگی میلگردهای تقویتکننده، محصولات زنگزدگی میتوانند باعث افزایش حجم میلهها تا شش برابر فولاد اصلی شوند. این امر باعث افزایش فشار بر روی مواد اطراف میشود که بهآرامی بتن را دچار ترک میکند. ازاینرو، در طول سالیان متمادی، ترکهایی در سطح بتن ظاهر میشود که منجر به ریزش و ضعیف شدن زیرساختهای بتن میشود. با انواع روش های جلوگیری از زنگ زدن آهن در این لینک آشنا شوید.
اهمیت تقویت میلگرد
میلگردها به سبب خورده شدن و یا زنگزدگی، لایه محافظ خود را ازدستداده و این امر سبب تضعیف خواص میلگردها شده و آنها را شکننده میکند. همچنین افزایش تنشهای داخلی در میلگردها به سبب وقوع خوردگی در آنها میتواند استحکام کششی آنها را در برابر تنشهای وارده کاهش دهد و این ضعف در خواص، به بتن نیز وارد شده و سبب تخریب بتن نیز بشود.
بتن بهخودیخود دارای استحکام کششی مناسبی نبوده و بسیار شکننده است و میلگردها هستند که بهمنظور بهبود خواص کششی در بتن قرار میگیرند تا این ضعف بتن را برطرف سازند. بنابراین، چنانچه میلگرد در بتن دچار ضعف و خرابی شود، تخریب بتن نیز دور از انتظار نخواهد بود. درنتیجه، مقاوم بودن میلگرد از اهمیت بالایی برخوردار بوده که علاوه بر جلوگیری و تأخیر در ایجاد خوردگی در آنها، سبب حفظ ساختار و یکپارچگی میلگرد شده و با حفظ خواص آنها، تقویت بتن به بهترین شکل ممکن را به دنبال خواهد داشت. با ضوابط کاشت میلگرد در بتن آشنا شوید.
روشهای تقویت میلگرد در برابر خوردگی
کنترل خوردگی در میلگردهای فولادی برای جلوگیری از آسیب و شکست میلگرد که شکست در سازههای بتنی را به همراه دارد، امری ضروری است. نزدیک به 40 درصد از شکست سازههای بتنی ناشی از خوردگی میلگردهای فولادی تعبیهشده در بتن است. دلایل زیادی برای خوردگی میلگردها میتواند وجود داشته باشد، اما بیشتر به کیفیت بتن، محیط و کیفیت شیوههای ساخت مربوط میشود. بنابراین اولین قدم در کنترل خوردگی میلگرد، ارائه کیفیت خوب بتن از طریق شیوههای ساختوساز خوب است. کیفیت مصالح بتن، تکنیکهای اختلاط، جاگذاری و تراکم و طرز کار خوب میتواند به کنترل خوردگی میلگرد کمک کند. بهغیراز مسائل مربوط به کیفیت بتن و ساخت آن، اعمال تغییراتی در میلگردها نیز میتواند به تقویت میلگرد در برابر خوردگی بسیار کمک کند. سایر روشهای تقویت میلگرد در برابر خوردگی به شرح زیر هستند:
استفاده از میلگردهای دارای پوشش کامپوزیتی سیمان-پلیمر
میلگردهای با پوشش پلیمری سیمانی که در بتن تعبیهشدهاند توسط یک محیط قلیایی احاطهشدهاند. بنابراین پوشش مبتنی بر سیمان برای کنترل خوردگی میلگرد سازگارتر است. بدین منظور نیز دو لایه پلیمر سیمانی روی میلگرد اعمال میشود تا یک پوشش بسیار مقاوم به خوردگی ب روی میلگرد ایجاد شود. رویکرد توسعه این سیستم بدینصورت است که فلز پایه میلگردها، حاوی الکترونهای پی است که بهراحتی در محیط خورنده آزاد میشوند و منجر به اکسیداسیون آهن و درنتیجه تشکیل اکسید آهن بهعنوان بازدارنده اصلی میشوند. بهمنظور جلوگیری از این اکسیداسیون، یک پوشش سطحی که قادر به برهمکنش/ باطل کردن الکترونهای آزاد شده است، ارائه شده است. میلگرد فولادی تقویتکننده در بتن در طول عمر مفید، در معرض یک محیط قلیایی قرار میگیرد و این امر مستلزم معرفی یک لایه پوشش است که باید با آستر و محیط قلیایی سازگار باشد.
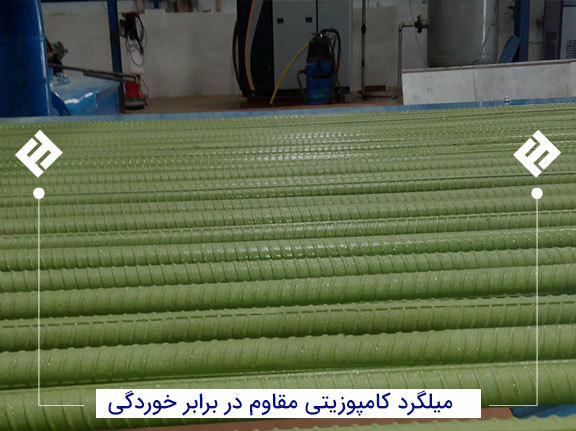
استفاده از میلگردهای با پوشش اپوکسی فیوژن
میلگرد با پوشش اپوکسی فیوژن، بهصورت 100 درصد از ذرات پودری که ذوب شده و آسیاب شدهاند و سپس جامد شدهاند، تولید میشود. این ذرات ذوب میشوند تا یک لایه چسبنده پیوسته در هنگام گرم شدن ایجاد کنند. در مورد میلگردهای پوشش اپوکسی فیوژن، هیچ فیلم پرایمر غیرفعال کننده ارائه نمیشود. پوشش اپوکسی پیوندی فیوژن باعث ایجاد ضعف در مسیر پیوند بین میلگرد و بتن قلیایی میشود.
استفاده از میلگردهای تغییر شکل یافته فولادی مقاوم در برابر خوردگی
مکانیسم مقاومت در برابر خوردگی در این نوع میلگردها، با تشکیل لایه اولیه اکسید محافظ یا زنگ شروع میشود. برخلاف زنگزدگی روی میلگردهای معمولی، زنگزدگی در این نوع میلگردها به شکل غیرفعال، مقاوم و خود تجدیدشونده است. اکسید محافظ دارای بافت ریز، چسبندگی محکم و مانعی در برابر رطوبت، اکسیژن، دیاکسید کربن، دیاکسید گوگرد و کلرید است که بهطور مؤثر از خوردگی بیشتر جلوگیری میکند. رسوب روی میلگردهای فولادی معمولی، به صورت اکسید پوستهپوسته با بافت درشت است که از رسیدن رطوبت یا اکسیژن به میلههای زیرین و ادامه خوردگی جلوگیری نمیکند.
استفاده از میلگردهای فولادی ضد زنگ و یا میلگردهای با پوشش گالوانیزه
فولاد ضد زنگ به سبب برخورداری از حداقل 5/10 درصد کروم، مقاومت بسیار خوبی در برابر خوردگی از خود نشان میدهد و چنانچه میلگردها از این نوع فولاد ساخته شوند، تا حدود زیادی میتوان از خوردگی و زنگزدگی در آنها جلوگیری کرد. ضمن اینکه، اعمال پوشش گالوانیزه بر روی میلگردهای فولادی باعث ایجاد یک لایه محافظ بسیار خوب از جنس عنصر روی میشود که قابلیت مقاومت به خوردگی را در میلگردها بسیار بهبود میبخشد.
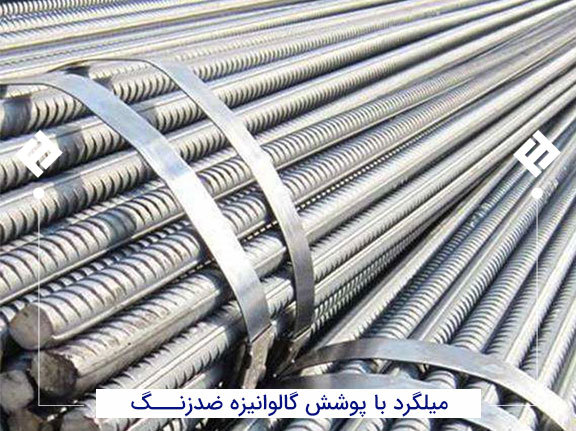
سؤالات متداول
1- تقویت میلگرد به چه منظور انجام میشود؟
میلگردهای فولادی به دلیل تماس مستقیم با خاک و یا بتن که از مقدار زیادی آب ساخته میشود، در معرض خوردگی و زنگزدگی قرار داشته و برای جلوگیری از صدمات ناشی از این پدیدهها، تقویت میلگردهای مصرفی در ساختوسازها از اهمیت بالایی برخوردار است.
2- خوردگی میلگرد تحت چه شرایطی اتفاق میافتد؟
برای ایجاد خوردگی در میلگردها، باید یک عامل اکسیدکننده که در اکثر مواقع همان آب است، وجود داشته باشد. همچنین، بهکارگیری میلگرد تحت شرایط نامساعد جوی و یا در محیطهای شور، احتمال وقوع و افزایش نرخ خوردگی در میلگردها را تسریع میبخشد. کربناتها و کلریدها دو عامل رایج از شرایط خوردگی میلگرد هستند.
3- بهترین روش تقویت میلگرد چیست؟
بهمنظور تقویت میلگردها، میتوان از استنلس استیلها و یا اعمال پوشش و بهخصوص پوشش گالوانیزه استفاده کرد. پوشش دهی گالوانیزه و یا پوششهای اپوکسی فیوژن بهترین روش تقویت میلگرد هستند.